Project Planning 101: Pre-Construction
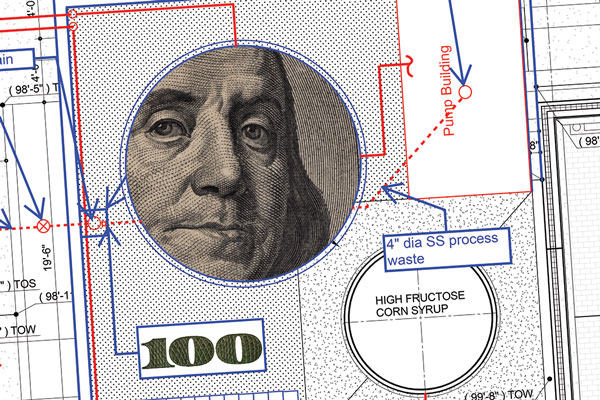
1 year, 7 months ago
Owners who get their builder involved during the design phase of a project can expect better outcomes for budget, schedule and quality.
By Craig T. Neises
Carl A. Nelson & Company
Through a process of master planning, it has become obvious that your organization needs to renovate and/or grow its footprint in order to best achieve your mission. And after considering issues such as where to build, what to build and how much to spend, you have arrived at the point of beginning the detailed designs and budgets that will lead to a specific project.
In short, you’ve reached the pre-construction phase.
Pre-construction is where you settle on the specifics of what to spend and how best to spend it. Here in Part 3 of our series, Project Planning 101, we will address this all-important stage of project development — the last phase before contracts are awarded and the construction commences, and when an Owner is able to make best-value decisions based on the expertise of the Construction Manager (CM) or Design-Builder that will stand to produce the lowest-cost, best-built and most-efficient finished project possible.
Many areas influence these outcomes, such as Building Information Modeling and clash detection; and retro-commissioning of existing mechanical, electrical, plumbing and technology systems. The most crucial are discussed below: pre-construction scheduling; budgeting and estimating; value engineering; design and constructability review; and code review.
Pre-Construction Scheduling
The schedule is the basis for keeping the construction moving forward and completing the project on-time. But scheduling also is an important part of pre-construction planning because it gives the project team a framework for identifying fast-tracking opportunities; recognizing and responding to potential equipment and material procurement challenges due to seasonal issues or supply-chain problems; and maintaining a time-sensitive process in the design phase.
Budgeting and Estimating
By developing increasingly detailed budgets at each stage of design (schematic, design development and construction documents), the project team is able to better manage the project plan relative to the available funding. Having detailed cost information enables the team to adjust designs, materials and equipment and schedule before bids are let and contracts are awarded. Because after that point, changes become either more expensive or more impactful on project scope.
Cost estimating — the domain of the construction manager or design-builder — not only drives the budgeting process, but also is key to Bid Day preparations. Estimating helps make bid results more predictable, which can aid in boosting bid participation from contractors, or encourage preparation of alternate bid packages to add or subtract from the project depending on bid results.
Value Engineering
Contrary to the too-common view, value engineering does not equate to looking for ways to save the project after bids come in too high. At its best, and most beneficial, value engineering is a process that takes place throughout pre-construction with the goal of providing the best value proposition to the Owner.
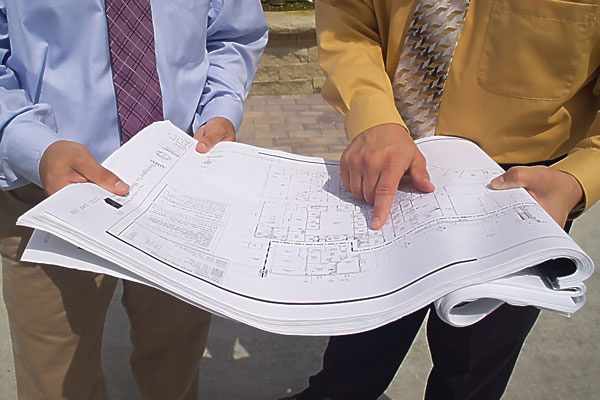
A Carl A. Nelson & Company project manager reviews pre-construction drawings of a hospital project. A builder's perspective at this early phase allows for alterations to be made in the design at a time when the cost to make changes is lowest. CANCO photo
This is achieved by looking continuously for design, material, equipment and schedule opportunities that reduce up-front construction cost as well as long-term operating expense, without making unnecessary sacrifices to project scope or quality. In traditional design-bid-build construction, contractors bidding based on completed designs have little opportunity or incentive to offer value engineering recommendations.
The ease of identifying value engineering savings depends on when the builder gets involved with the project. In a constructor-led design-build project, or when a CM is engaged at or near the outset of project design, value engineering takes place throughout the process and can be difficult to separate from other design decisions. By comparison, a pre-construction contractor hired late in design may have more opportunity to identify big-ticket, scope-preserving sources of savings.
Design and Constructability Review
Along with value engineering, design and constructability review is a process that takes place throughout pre-construction to ensure the project can be built as-designed with quality and efficiency. This process includes ensuring construction standards are met by the design, that systems are compatible and Owner intent is being met by the design.
This review process also enables a builder working in the pre-construction advisor role to determine whether scheduling of heavy equipment on the site creates opportunities for other design choices that may create value by saving time or money on the project. Review of as-designed efficiency of ongoing maintenance of the finished project also takes place at this time.
Code Review
Expert review of building, life safety and other code requirements ensures code requirements are met by the design, which prevents headaches later during construction and closeout, when a failed inspection can cause significant delays or added costs on a project. Just as important is understanding what the code does not require for a particular use or space. Being equipped with this knowledge during pre-construction allows for avoiding extra cost on unnecessary design features or systems.
Pre-Construction Pays
Whether with a design-builder or construction manager, the benefits of engaging a pre-construction advisor commonly pays for itself and then some, as the cost, schedule and constructability expertise of the builder is brought to bear early in the process when changes can be made at the least cost.
Carl A. Nelson & Company, founded in Iowa in 1913, has decades of experience in construction management and design-build construction. Our construction project managers, engineers and code experts are available to help your organization get the best value for the investment on its next construction project. To learn more, contact Dan Culp at (319) 754-8415, or write to canco@carlanelsonco.com.